In 2007, Shell discovered the Prelude natural gas field in the Browse Basin north of Western Australia. Combined with Concerto, another area discovered in 2009, these two fields hold around three trillion cubic feet of liquids-rich gas.
The finding led to the Australian Government approving plans for the Prelude FLNG, which stands for floating liquefied natural gas, in 2010, something that – millions of hours spent on engineering and design later – is set to see Shell complete one of the world’s largest projects of its kind in the next year.
So, let’s take a look at what the FLNG is exactly and how this could impact global industries.
“This is revolutionary technology developed by Shell,” Neil Gilmour said.
What is the FLNG?
The FLNG is Royal Dutch Shell’s attempt of transforming how natural gas resources are developed.
Designed to recover offshore resources that would be too costly or difficult to source without pipelines or land processing plants, the Prelude will be the largest facility ever constructed. A joint venture between Royal Dutch Shell, INPEX, KOGAS and CPC Corporation, the vessel is being built in Geoje, South Korea by the Technip/Samsung Consortium (TSC)
“This is revolutionary technology developed by Shell,” Neil Gilmour, Shell vice president integrated gas development suggests. “It has the potential to change the way we produce natural gas.”
It allows the production, liquefaction, storage and transfer of liquefied natural gas at sea, as well as the capacity to process, condensate and export liquefied petroleum gas.
Details about the vessel
Once completed, the Prelude FLNG will be a 260,000 tonnes heavy, 488 metres long and 74 metres wide vessel – able to displace more than five times the volume of a US Navy Nimitz-class aircraft carrier.
It took thousands of workers 12 months to construct the Prelude FLNG’s 200,000 tonnes hull at Geoje’s Samsung Heavy Industries (SHI) shipyard – one of the few dry docks in the world big enough to construct at this scale. At Geoje, where more than 5,000 people work on the project each day, topside modules the size of a typical offshore platform are now being installed and integrated with the hull.
As Shell’s first deployment of its FLNG technology, the facility is set to cool produced gas to -162 degrees, decreasing its volume 600 fold. The vessel itself is designed to withstand even the most severe weather, including millennial storms of category five cyclones.
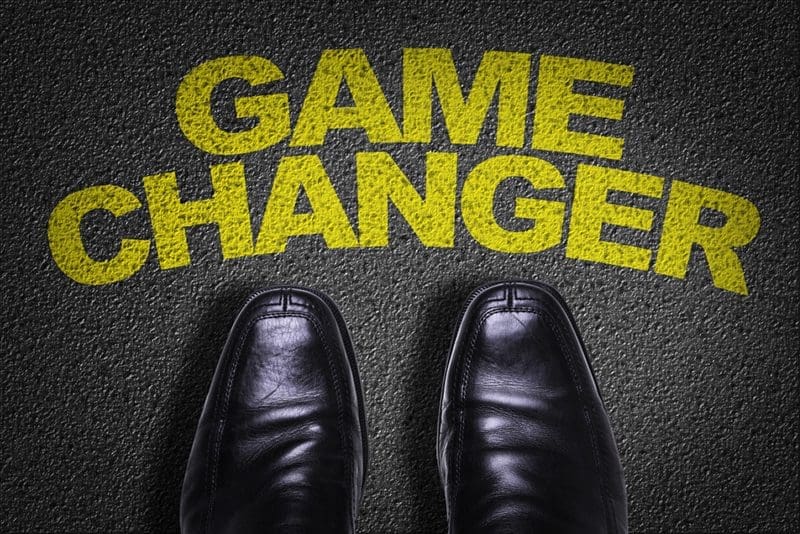
What does this mean?
This year is set to see groundbreaking developments with the implementation of the FLNG, something that will affect more than just the global gas industry. The incredible engineering feat the facility symbolises has the potential to influence how construction and design of such super-vessels is approached in the future.
One thing we know for sure, is that businesses wanting to stay ahead of the curve need to be proactive and ensure their own industrial equipment – whether it is custom engineered or not – performs as effectively and efficiently as possible.
At SRO, we offer expert advice as to the best solutions for your operation. Brand-agnostic, professional and experienced, our team can help your organisation remain successful. Reach out to us today for more information.
Recent Comments