Manufacturers and other organisations that rely on industrial-grade equipment are at the mercy of that machinery. Industrial equipment deals with a lot of wear and tear over time and constant use, and when it finally breaks down, operations could come to a screeching halt.
Between production stoppages, equipment repairs, component replacements and other related expenses, the costs of malfunctioning machinery can quickly spiral out of control. According to some estimates, the total cost of industrial equipment failure is anywhere from four to 15 times the amount spent fixing that machinery.
Industrial operators need to get production up and running again as soon as possible, but replacing equipment out right isn’t always financially feasible. Organisational leaders will need to determine when the time is right to repair broken equipment or replace it altogether.
Low on funds? Repair first
Industrial machinery is expensive, costing thousands of dollars for the equipment alone, not to mention installation fees and configuration fees. Equipment failure can happen at any time, and not all companies will have the capital on hand to pay for a replacement at a moment’s notice.
If your organisation hasn’t budgeted for unforeseen machinery malfunction, your only recourse for replacing broken equipment could be to agree to financing terms that will cost the business far more in the long run.
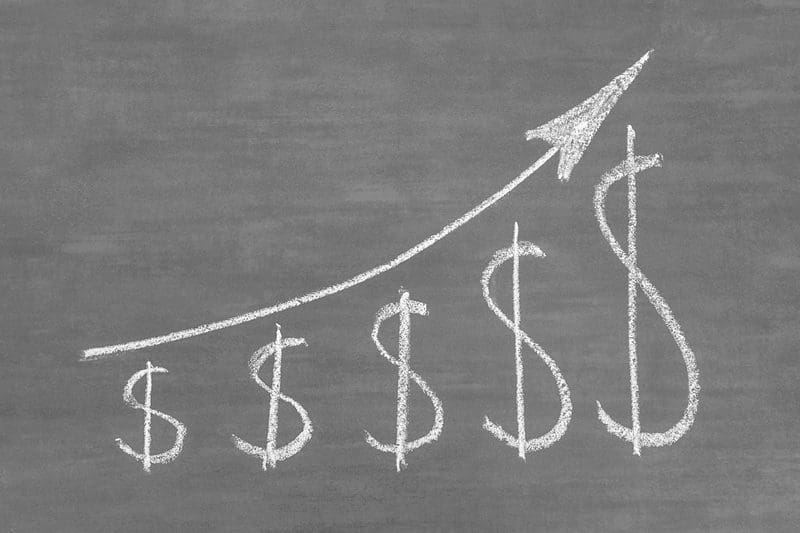
Rather than swap out broken-down equipment in that scenario, it can be advantageous to try and repair any components that have stopped working. Repair costs are far less than purchasing new hardware, and are easier to budget for.
Repair when time constraints are a concern
Manufacturers can’t afford to wait days or weeks for new equipment to be delivered and installed. Every minute that passes with a broken-down piece of machinery is lost production time. Getting production ramped up again as quickly as possible should be your primary concern in order to soften the hit to your bottom line.
Repairing broken components in a larger piece of machinery, in all likelihood, will take less time than replacing the equipment. That means your operations will be up and running quicker with fewer production delays.
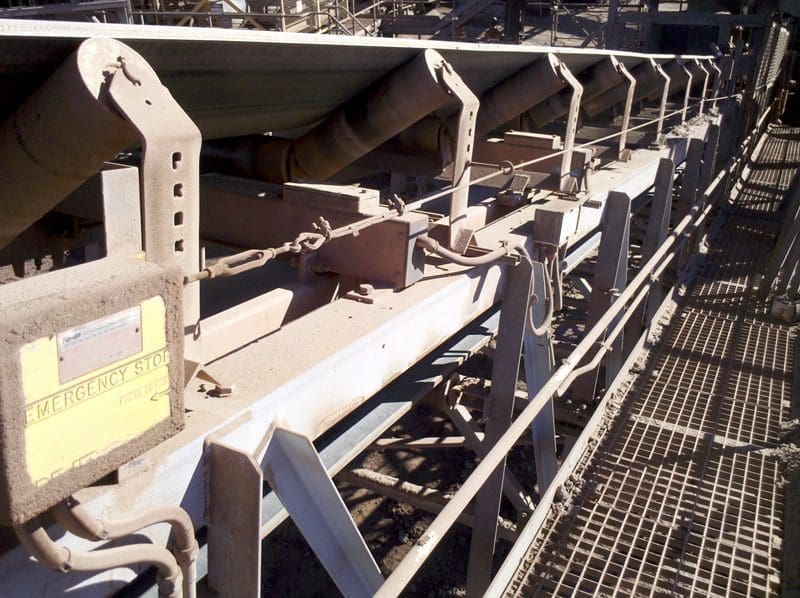
Save replacement as a last resort
When all else fails, consider replacing the malfunctioning machinery with a brand-new piece of equipment. If the underlying problem is more systemic than one or two broken components, if the equipment has exceeded its intended shelf life or if repeated repairs have done little to correct the problem, it’s time to consider a replacement.
Due to the high costs of industrial equipment, it’s usually wise to hold off on making such a dramatic decision without first exploring all other possible options. Running a cost-benefit analysis could show that a simple on-site repair is the best course of action, or it could determine that a wholesale replacement is needed.
You don’t need to handle analysis on your own. SRO Technology’s experienced team can expertly assess your malfunctioning industrial equipment and identify the underlying problem. We’ll consult you every step of the way, even if you need a full-scale equipment replacement. Reach out to SRO Technology to find out more.
Recent Comments