Maintenance & Calibration
Belt scales, Bin level indicators, tramp metal detection solutions, proximity switches, pressure sensors and other devices provide clarity of material quantity and quality within complex operations. The mining, food processing, wood and pulp, energy production and chemical manufacturing sectors all depend on information to sustain their operations. Various sensors supply that data on a continuous basis, but what if they’re generating inaccurate readings?
SRO Technology provides comprehensive maintenance and calibration services to companies participating in a wide range of industries. Specialising in multiple brand-name instruments, we assess and adjust sensors to ensure your processes are supported by dependable devices.

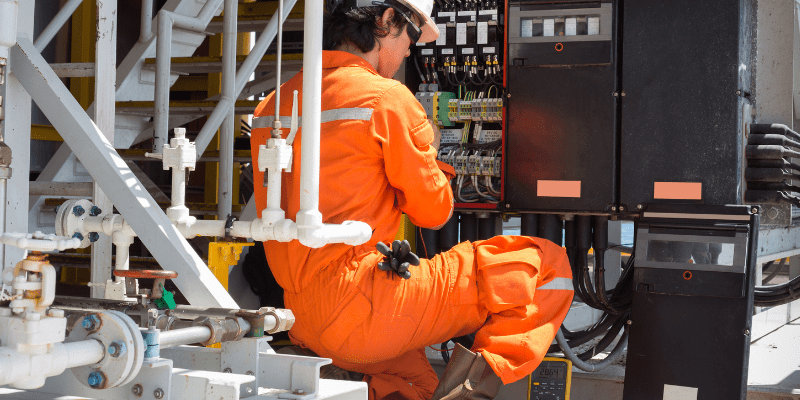
Delivering insight into complex operations
For the most part, consumers have little idea as to how a factory takes raw materials and turns them into the products they use on a daily basis.
However, the people in charge of such operations must understand their intricacies, and address minor inconsistencies in sensor calibration before they create major cost and quality issues. Consider the importance of the following solutions:
- Belt scales measure, Monitor and control material flow along conveyor belts.
- Tramp metal detection systems remove unwanted bits of metal from mineral processing, pulp manufacturing and food processing operations. This not only ensures optimal product quality, but also prevents equipment failures.
- Load Cells are used in products such as weigh belt feeders. These control how much material is fed into a process, a key function when manufacturing products made up of multiple substances. They enable facility managers to enforce quality assurance standards, even in the most complex operations.
- Level measurement sensors register the amount of product an operation handles by the minute. They use laser, radar, ultrasonic and gravemetric technologies to calculate the amount of material a facility produces in a given day.
What if a coal mine’s level measurement devices told managers the facility had processed 4,200 tonnes of material in a given, day when it had actually produced 4,250 tonnes? The average person may view this discrepancy as a minor flaw, but to a facility operator, this inconsistency could mean thousands of dollars in unrealised revenue.
Why SRO Technology?
No matter what industry you compete in, our technicians are prepared to accommodate. We specialise in sensors used by iron ore and coal mines, power stations, wood mills, rubber factories, recycling plants and food processing facilities.
Upon contracting SRO Technology, we’ll establish a well-structured maintenance and calibration schedule to check up on your operations as necessary. Whether you want monthly or yearly assessments of your instruments, we’re prepared to accommodate.
As a part of our maintenance and calibration services, we Audit and deliver informed recommendations as to how you can better use your sensors.
Whether you’re working at a liquefied natural gas processing plant in Victoria, a copper mine in Northern Territory or a granary in Queensland, our technicians are there to assist you. We have service centres spread across the nation, ensuring we can respond quickly to whatever requests you may have.
Our ultimate goal is to help you establish and maintain cost-effective solutions that improve your operations. If you’d like to know more about our services, contact us at 61 2 9525 3077, or send an email to sales@srotechnology.com.