As a general rule of thumb, mining equipment is built to last. It needs to be incredibly durable to keep up with the rigorous work it's used for. Mining equipment gets put to use day in and day out, whether it's used for drilling and breaking up pieces of rock, for hauling tonnes of industrial buckets filled with ore and other materials or to crush and pulverise chunks of rock.
This machinery may be resilient, but it isn't indestructible. During the course of normal operations, drill bits can crack, digger teeth can fracture and chains can break. That material – tramp metal – then falls onto conveyor belts mixed in with ore, rock and materials slated for processing.
Tramp metal may seem like a trivial nuisance, but it, in fact, poses a major threat to mining operations. Site managers need to take every recourse available to identify and remove tramp metal from their conveyors. Consider these three reasons tramp metal puts mining businesses at risk.
1. Tramp metal can damage equipment
Probably the most pressing reason to make tramp metal removal a priority is the threat this material poses to critical mining equipment. Small pieces of debris like driller rods, shavings, nuts, bolts and chains can cause damage to even the most durable industrial machinery. Such seemingly insignificant bits of metal could easily harm a jaw crusher, requiring extensive repair or replacement. Tramp metal could also get lodged in a conveyor belt, impeding production and causing extensive damage to critical site machinery.
Such maintenance is expensive and time-consuming. While repairs are made, operations have to grind to a halt. Every minute, hour and day that your site is shut down impacts the business's bottom line. Factoring in all expenses related to equipment repair or replacement and production downtime, even a tiny bit of tramp metal could cost mining businesses an enormous amount of money.
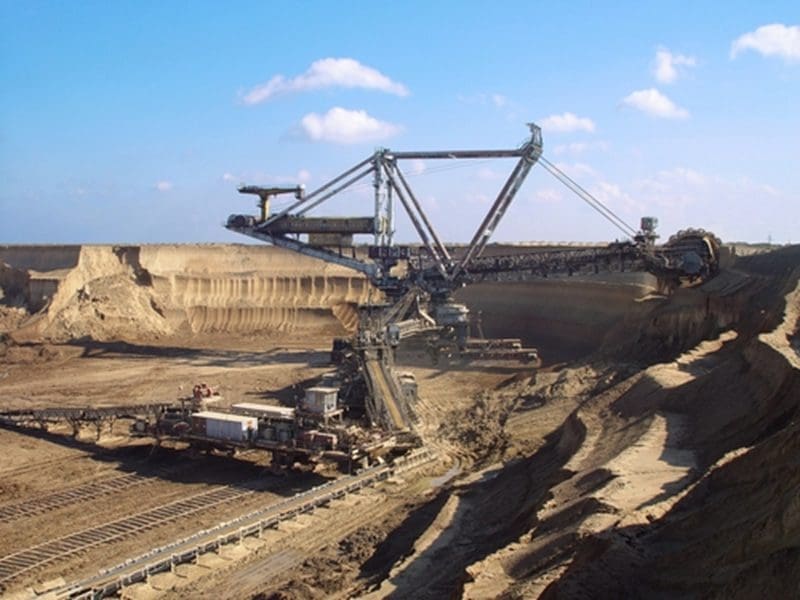
2. Work safety could be at risk
Mining is often dangerous work, with employees routinely operating heavy machinery on rough terrain. The slightest mistake could have fatal consequences. Mining operators do their due diligence to protect employees from the hazards of the job, but it's easy to overlook the threat that a broken chain, loose nut or metal shaving poses if it passes through conveyor belts and is processed along with rock, ore and other material.
In one instance documented by West Australia's Department of Mines and Petroleum, an errant ripper boot from a bulldozer became lodged in a jaw crusher. When the equipment operator inspected the malfunctioning machinery, the tramp metal was ejected with enough force ricochet off the control cabin 15 metres away as well as an adjacent steel beam and land back into the crusher's jaws. Luckily, the projectile missed the operator, but an investigation into the incident concluded that it could have very well caused a fatally had the tramp metal made contact.
Mining operators need to account for every detail when promoting worker safety, and they cannot overlook the importance of removing tramp metal.
3. Tramp metal can affect production and output
As noted, tramp metal can damage machinery and cause production stoppages, but it can also impact the quality of a site's output. Without a mechanism to identify and remove this material during the extraction process, mining businesses could be shipping out ore, minerals or other valuable substances that are tainted with tramp metal.
Output quality is extremely important to maintaining a good reputation in the mining industry. Proactively removing impurities and scrap metal from your final product will lead to more satisfied customers who continue sourcing their materials from your mining operation.
SRO Technology continues to provide the very best equipment to the mining industry, offering high-quality products from trusted brands like Thermo Fisher. Contact our team to learn more about our service and how we can help improve your mining business.
Recent Comments