Tramp metal presents a major problem for mining and industrial operations, potentially damaging expensive equipment and setting back production schedules. During the normal course of extracting ore, coal and other materials, pieces of metal from machinery and tools such as nuts, bolts, chains, digger teeth and bucket shovels can mix with the raw materials. If left unchecked, that tramp metal can go on to damage even high-volume industrial crushers and conveyors.
Detecting tramp metal before it reaches that machinery is essential. If you run into problems detecting tramp metal, follow these steps to avoid expensive equipment breakdowns and repairs.
Audit your machinery
If you see any sign that your tramp metal detector is malfunctioning, do not hesitate to run a thorough audit of your machinery. Even small pieces of debris can cause enormous damage to expensive equipment, so it's imperative that facility operators act quickly to avoid costly repairs or replacements.
Conduct an audit, either internally or with third-party assistance, to determine if all tramp metal detectors are running properly and catching unwanted materials on conveyors before they reach other processing equipment. A comprehensive audit will bring any issues to light and give site operators the information they need to determine if they need to calibrate machinery, repair a faulty component or replace the tramp metal detector altogether.
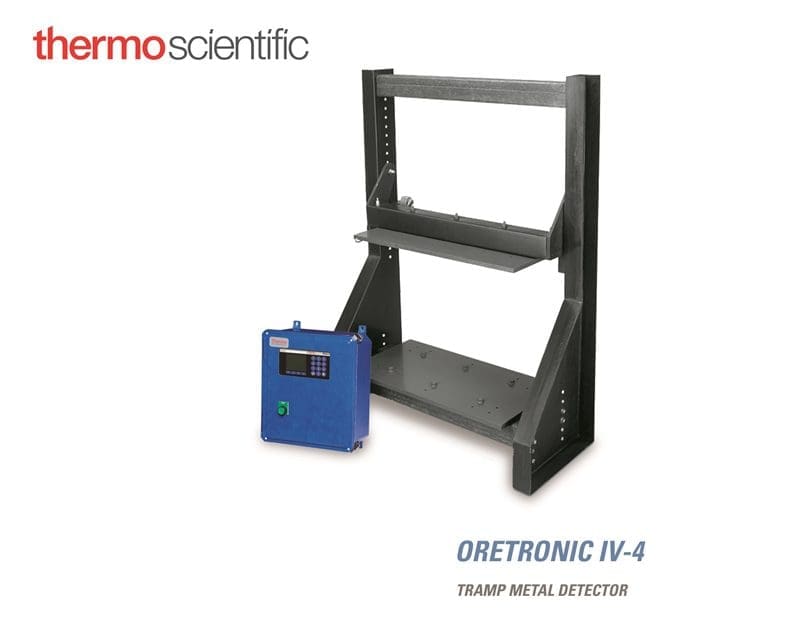
Contact a specialist
Given the high stakes of tramp metal detection, it's extremely important that this equipment operates with total accuracy and reliability. Once you have spotted a problem with your machinery, it's time to bring in qualified specialists to repair or replace the faulty equipment.
Not all metal detectors are suitable for industrial and mining operations, considering the various types of metallic objects and materials that run along conveyors in these environments. Metal detector systems that are created for specific applications outside of mining industries may not catch debris like manganese steel mantles.
Even within industrial applications, different organisations will have different tramp metal detection needs. Coal mines, for instance, frequently deal with finer materials like swarf that can fall onto conveyor belts, which requires a more sensitive and finely calibrated setup.
Consult an experienced service provider to find the right tramp metal detector for your operation. SRO Technology has provided high-quality equipment and auditing services to the mining industry for years. Our expert (OEM trained) teams can diagnose tramp metal detection problems and recommend whatever changes are necessary. Contact our team to learn more.
Recent Comments