Streamlined process flows are essential for business success and are increasingly becoming the bread and butter of operations managers' daily activities.
How does warehouse design play into this though and what steps can you take to improve overall productivity?
Whenever a staff member moves an item, it costs the business money.
The importance of design
Disorganisation can be the death of productivity. And poorly laid out warehouses are notorious for wasting time, therefore sucking money.
Whenever a staff member moves an item between receiving and dispatch points, it costs the business money. This means products arriving at your warehouse need to move swiftly from the goods-in point to the first relevant work station, ideally in a streamlined process rather than random selection to reduce motion time.
Warehouses that are designed to work around a business' specific needs reduce motion and transportation actions within process flows, therefore allowing workers to complete work in a much more efficient way.
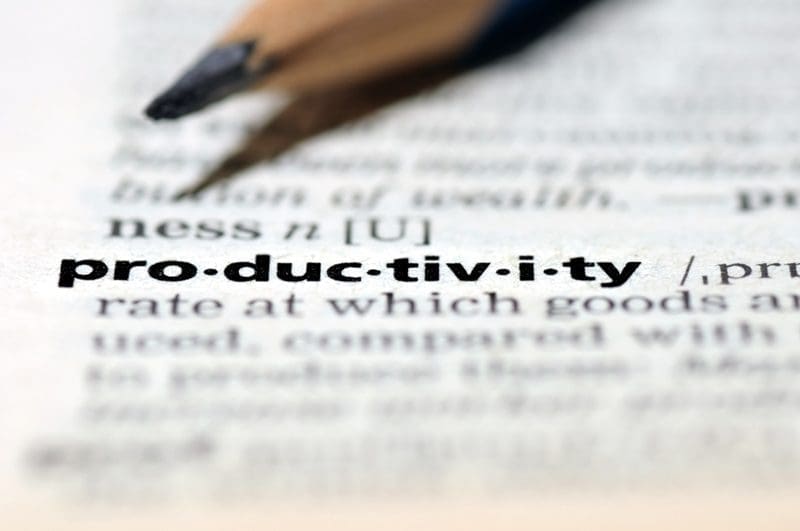
How can you improve productivity?
Manufacturing Global points out that designing warehouses with designated areas for each action is the first step to reducing turnaround time. With that, vertical optimisation of the space available will use resources much more effective than paying for more floor space.
Smart storage solutions allow the bundling of relevant SKUs and reduce the time items spent sitting idle while staff try to either find a specific product or determine where the next work station is. Leading from this, Inbound Logistics has some additional suggestions to compliment general warehouse design considerations:
- Process standardisation: Reducing potential variation in unloading, shift schedules or facility management through streamlined process flows also decreases the likelihood of errors while saving time and money.
- Employee empowerment: The people that are on the floor each day will be able to help reduce waste the most effectively. It's therefore important to involve them in the process of improving processes and warehouse design. An added bonus is that good staff engagement usually results in better productivity as well.
- Leadership education: Asking the right questions, collecting information and taking corrective action needs to follow streamlined processes just as much as on-ground activities. Educating the leadership team on expectations and processes is a crucial part of this.
- Variation, not averages: Six Sigma teaches us that a more stable and predictable process – which also improves productivity – reduces variance of actions. It's all about continuity and reliable ways of fulfilling tasks.
- Include the TAKT time: To achieve a steady flow with standardised instructions, incorporating the TAKT time is a must. Specifying the absolute maximum cycle time a product is allowed to meet demand enables better target setting, which in turn can help operators identify improvement opportunities.
- Focus on training: Incorporating a robust training program for all employees will enable associates to break down and teach new team members their jobs in a more effective way than the usual "learn-as-you-go" method.
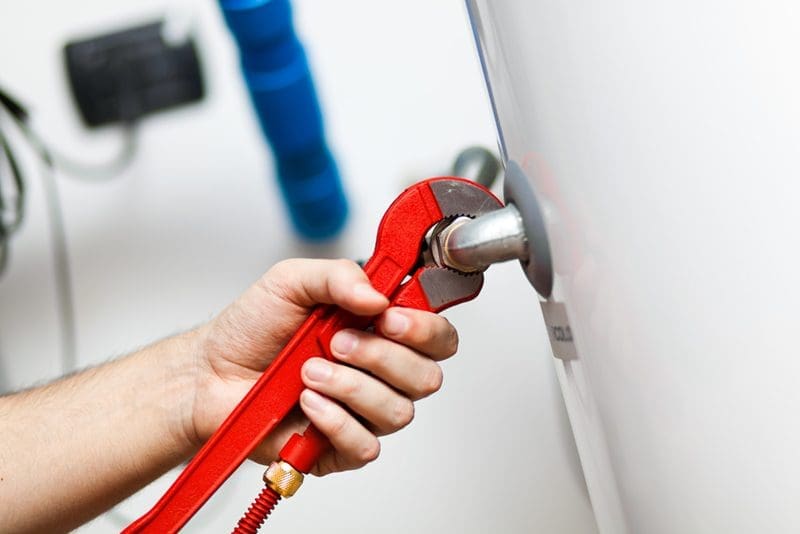
Take care of instruments and machinery
Another way of improving productivity and output rates is to ensure equipment is maintained well and updated if needed. It's a logical conclusion that staff won't be able to accomplish their workload or run risk of injury when using the wrong or outdated tools.
Rather than going out and buying new machinery for the sake of it though, it's better to evaluate whether current machinery simply needs to be refurbished or serviced. Training employees on the safest methods of using instruments and new equipment is just as essential when it comes to preventing accidents and improving capacity.
One last thing to remember is that no matter how advanced your warehouse is currently, good operations reassess and evaluate processes regularly to ensure streamlined flows are maintained and improved.
At SRO Technology, we can help you improve productivity by providing the expertise to engineer, manufacture and service all the measuring instruments you need – from density gauges to belt scales. Reach out to our team today to talk about your specific needs and find out what we can offer you.
Recent Comments